OUR FOCUS DURING THIS PANDEMIC
For the past two months the Jiobit Hardware Team has been working tirelessly to create PPE solutions for our healthcare and essential workers during this pandemic. With the anticipated PPE shortage and current demand outstripping supply, the team focused on solutions that use standard off-the-shelf parts and 3D rapid prototyping to create face shields and powered air purifying respirators (PAPR) systems that can be assembled easily and anywhere in the world.
[JIOBIT CUSTOMERS CAN APPLY FOR FREE JIOBIT PAPR]
What is a PAPR?
POWERED AIR PURIFYING RESPIRATOR
A PAPR provides protection from environmental particulate contaminants by delivering a steady flow of filtered air (HEPA Filter - 99.97 Efficiency) into the mask or hood vs lung power (N95 mask). This minimizes CO2 re-inhalation and prevents fogging and allows workers to be in contaminated areas for longer periods of time. Additionally, it can accommodate limited facial hair and protects eyes and face from debris vs a standard N95 mask. Using a tight fitting face-piece can also provide an assigned protection factor that is up to 100x greater than an N95 mask.
The PAPR has a filtration assembly containing a HEPA filter, blower motor, battery pack and speed regulator (to provide constant air flow), a connecting hose and a receptacle to attach to a mask or a hood.
This is our low-cost PAPR that can be used with two types of masks and hoods.
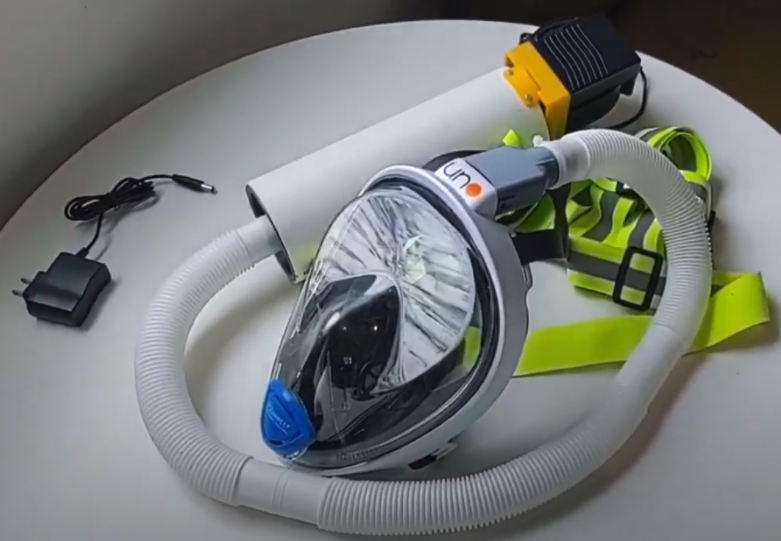
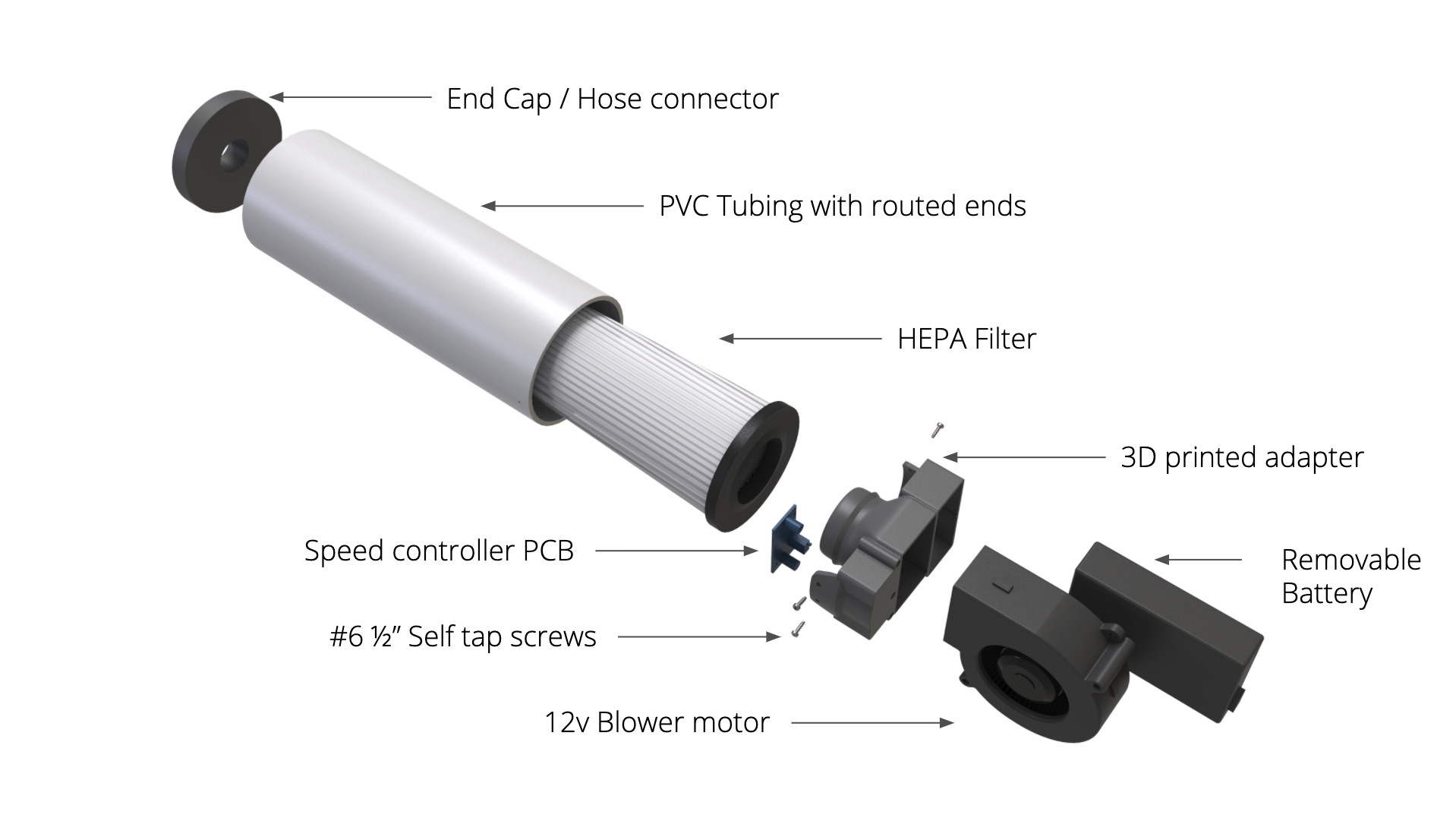
SPECIFICATIONS
- Airflow: ~7 CFM (cubic feet per minute)
- HEPA Filter: 99.97% efficient down to 0.3 microns particle size. Standardized replaceable HEPA filter cartridge allows for economical replacement when required
- Battery: Rechargeable 3000 mAh Li-ion. Standardized/non-proprietary battery allows for affordable additional packs
- Battery Voltage: 12V
- Battery Charge Time: 8-12 hours
- Battery Run Time: 4-6 hours
- Weight: 2.3 Lbs (excludes mask)
- Cleaning: Standard disinfectant wipe down, non abrasive only for mask lens
Behind the scenes
HOW WE DID IT
The Jiobit team has been meeting daily with other Chicago area engineers and problem solvers (from PDT, MPC, CH3 and mHub) to identify areas where we could make the biggest impact based on our expertise, our access to available materials, our access to components and our access to equipment. We had to do this collaboration within the confines of the nation-wide lockdown and social distancing rules that are in effect.
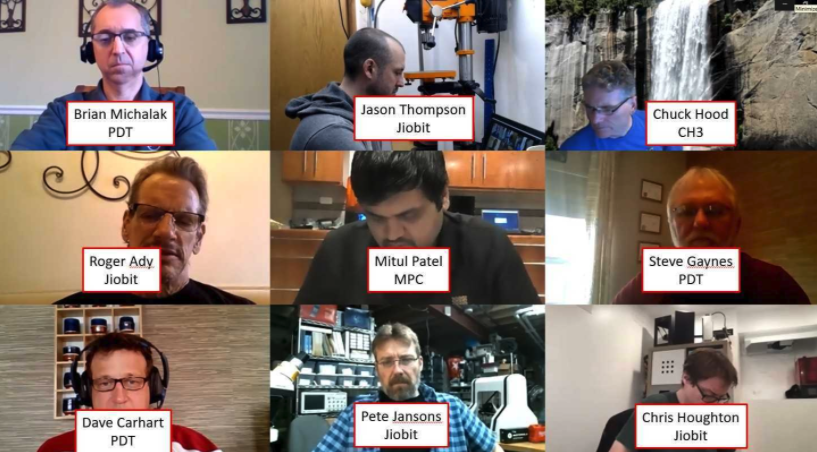
After a quick turnaround of our PPE Face shield that used a simple 3D printed frame and office supplies to complete the shield, we focused our attention to the PAPR system leveraging our capabilities with the following goals (in order):
- Functionality-- provide better ingress filtration than an N95 respirator, 4 hours or more of battery life, and maximum comfort for the user
- Speed-- address the immediate gap in the availability of this equipment
- Component flexibility-- roving supply chain component outages and extremely delayed shipments ( individuals and companies compete for the same components) demand supply chain agility
- Styling and cosmetics-- not a priority
CONCEPT LOCKDOWN
Other Chicago Rapid Response engineers and developers, as well as medical professionals in the respiratory illness field, were brought in through our daily mHub/Matter/1871 collaboration to help vett design concepts. The Miro collaboration tool allowed the teams to quickly provide feedback and brainstorm further to refine the concepts.
By gravitating to a design based on off-the-shelf parts connected by a few custom rapid-prototyped couplers, we were able to produce working units quickly using in-stock parts available through local stores and internet-based wholesalers. The first late-night proof-of-concept (shown below) was quickly followed by a refined version from the next evening. This formed the basis for the final design.
Next we all fired up to manufacture and order components towards an assembly build within a few weeks. Our 3D printers ran around the clock during the development and testing process before building the first production run.
Given the stay-at-home orders in the area our homes were turned into 3D printing farms, inventory warehouses, and product validation labs (A BIG THANK YOU to those family members for “going with the flow” on this project).
TESTING AND CALIBRATION
With everything we do, we wanted to make sure that our solutions meet the needs and specifications required for safe and comfortable use. Using an anemometer, we identified the optimal operating voltage to the blower and adjusted the motor speed controller pot on each unit to deliver a constant and comfortable airflow that also maintained low velocity over the filter media to insure high efficiency.
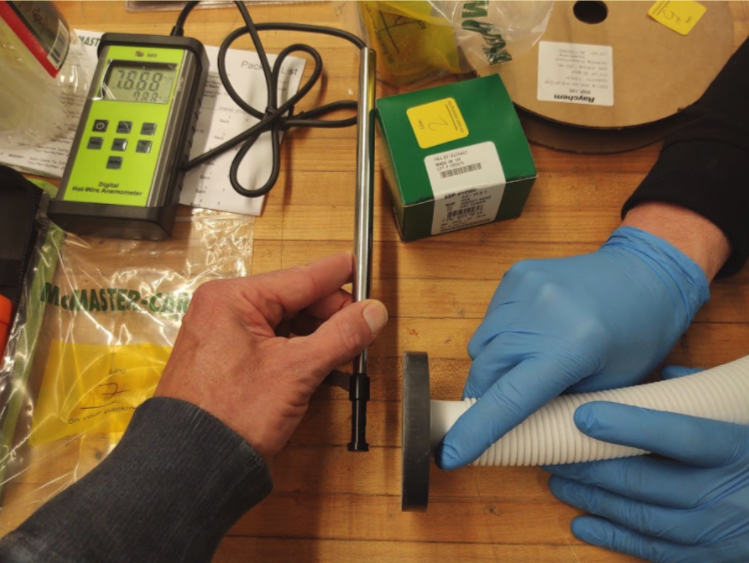
To help make sure only filtered air reached the user, we designed the unit to have elevated pressure within the filter and all the way downstream to the mask or hood such that any incidental leaks will only leak out filtered air and not introduce environmental contaminants. This is much different than designs that draw a vacuum on the filter such that leaks in that chamber or even the filter itself will introduce contaminated air. See the cross-sectional view below.
Finally, we ran a “burn-in” test to conduct the initial battery cycling and verify proper operation of each unit.
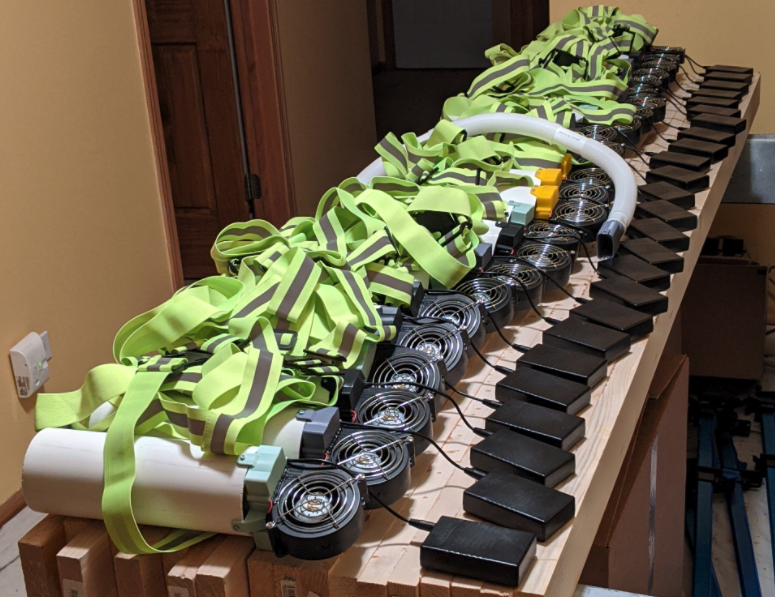
We are currently looking for healthcare workers, front line workers, care home workers or anyone working for VA that are in need of a PAPR and do not currently have access to the PPE they need. If you are someone in these fields or know someone working in these fields that could use one of these, please reach out to us.